CNC Turret Punching Machine
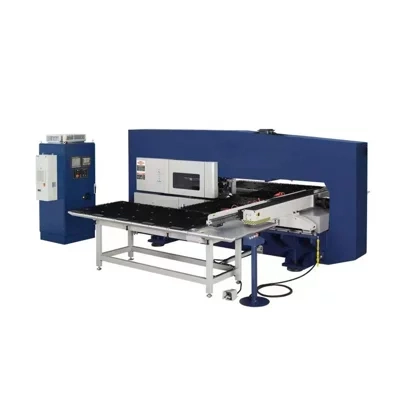
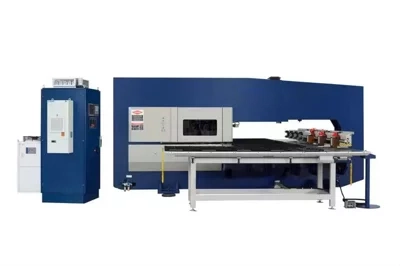
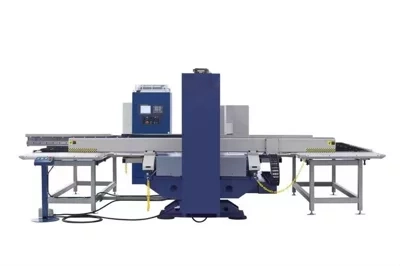
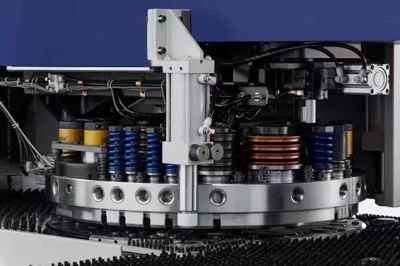
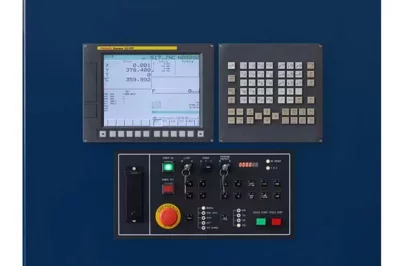
The new generation of MacTech turret punch is a low energy, high efficiency turret punch with low environmental and maintenance costs. The MacTech can be configured in 22- or 33-ton options. The MacTech was designed with a thick turret to ensure longevity of the machine and its tools and to minimize tool deflection. MacTech performs full punches, hovering, marking and forming operations. The KS model can be upgraded with our Ultra Package which can decrease part processing times by up to 40%.
The MacTech comes standard with the following features:
- Automatic Tool and Linear Components Lubrication System
- Pneumatic Ball Transfer and Brush Table for ease of loading/unloading
- Vacuum Assist System for slug removal
- 32 Stations 2 Auto indexing stations
- One Mirror-Type Safety System to guard entire work envelope
- Man-Sensors on moving tables
- Sheet Jam Protectors to detect warped material
- Sheet-gripper sensors to detect loose material
Main Technical Features
1/Single servo motor driven system, adopts large torque direct driven servo motor and driving unit with high overload capacity to realize low energy consumption, high transmission efficiency, reliable performance and convenient maintenance.
- Adjustable speed and stroke
- The punch stroke can be selected according to the thickness of the sheet automatically, improving the work efficiency.
- The punch speed is adjustable during each point of each single station,
- the machine can realize the high-speed swift during empty run and low speed during real punch, in this way, the punch quality can be improved effectively, and there is really no noise during punch.
- The system features with over-current protection and mechanical overload protection devices.
- The punch force can be automatically adjusted according to the sheet thickness and ram running speed to make the punching quality reach a high level.
2/The turret with bushing is process in pairs
The turret is processed by special device to ensure the coaxiality of the upper and lower turret and expand the service life of tooling; the bushed turret simplifies the turret structure to extend the service life; long tooling can be used to increase the guiding accuracy and expand the tooling service life (for thick sheet).
3/Imported pneumatic, lubricating and electric components ensure the reliability of the whole machine.
4/Large lead guideway and ballscrew from Japan or Germany ensures high feeding precise.
5/Hard brush and ball mixed worktable reduces the noise and vibration during running and also protects the sheet surface.
6/O-type welded frame has been vibrated for twice, the stress has been deleted completely. The frame is processed by Germany SHW dual-side pentahedron processing center at one time, no need to make second time positioning.
7/Floating clamp with large clamping force ensures the stable feeding; integrated carriage ensures good rigidity and convenient movement of clamp.
8/ The system is featured with the function of automatic clamp protection to avoid the damage of tooling and clamp, ensuring the continuous running of the program.
9/ The auto-index adopts high accurate worm wheel and worm mechanism, ensuring high precise indexing. The Max. tooling diameter can reach 88.9mm and the auto-index can be expanded to 4 nos.
10/ Integrated beam structure to make the carriage and beam into one part, increasing the rigidity and brings the accurate positioning. The machine can run much more stably during high-speed feeding and it puts an end to the deflection of X and Y axes.
11/ X axis: adopts servo motor to drive the high precise balls crew and the carriage is featured with high rigidity and lightweight design. Y axis: servo motor directly drives the feeding rack which is connected with the machine guideway, split type beam is fixed with feeding rack, and the acting force will be transmitted to machine frame & ground via feeding rack and guideway in order to reduce the self-vibration of the beam. This structure is featured with the characteristics of good rigidity, light in weight, low gravity, and good dynamic response in the entire feeding system, stable running and good precise.
12/ Central lubrication system is adopted to send the lubrication grease to the relative lubricating point directly, reducing the friction of each working pairs and increasing the service life.
13/ Anti-sheet-deformation switch and sheet-anti-stripping switch are adopted.
Loading And Unloading System
Main Specification
Item | Unit | Specification |
Max sheet size | mm×mm | 3000×1500/2500×1250 |
Min sheet size | mm×mm | 800×400 |
Thickness | mm | 0.8~3 |
Max sheet weight | kg | 105 |
Max position speed for horizontal loading | m/min | 80 |
Max position speed for vertical loading | m/min | 40 |
unloading position speed | m/min | 60 |
Max height for the loading store | mm | 220 |
Are pressure | bar | 6 |
weight | t | 6 |
Main Parts
ITEM | Configuration |
Girder model | Single-beam high-rigid truss + aluminum lightweight drive |
Guider way and driver model | Roller guide, rack and pinion driver |
CNC system | BECKHOFF |
Servo driver | PHASE |
Reduce gearbox | SEW/STOBER |
Chain | IGUS |
Centralized lubrication system | Standard |
Check the material | Standard |
Pneumatic parts | AIRTAC |
Vacuum element | AIRBEST/SMC |
Electrical parts | Schneider |
1. Cooperate with CNC punch to greatly improve the overall processing efficiency. When the punch is unloaded, the loading robot is ready, and the non-processing time of the punch is very short, which greatly improves the production capacity of the main machine.
2. The world's advanced truss robot structure is applied to the CNC punching machine for feeding and connection, which has stronger technical competitiveness.
The unloading unit adopts a cantilever structure, which has better openness, low driving center of gravity, and simple structure. The standard unloading can be shifted by 2 clamps to ensure the unloading of small materials (width 400mm and above); mobile brush bench It is assembled by aluminum alloy profile, driven by double rodless cylinder, light weight, smooth and beautiful movement.
The overall structure is compact and highly integrated: the integrated design of the loading truss, the control cabinet, the double measuring device and the pneumatic lubricating unit, and the unloading unit is connected with the electrical cabinet by a plug-in aviation plug, which is convenient for quick adjustment and overall hanging. Operation and improve efficiency.
The unloading unit adopts a cantilever structure, which has better openness, low driving center of gravity, and simple structure. The standard unloading can be shifted by 2 clamps to ensure the unloading of small materials (width 400mm and above); mobile brush bench It is assembled by aluminum alloy profile, driven by double rodless cylinder, light weight, smooth and beautiful movement.
The overall structure is compact and highly integrated: the integrated design of the loading truss, the control cabinet, the double measuring device and the pneumatic lubricating unit, and the unloading unit is connected with the electrical cabinet by a plug-in aviation plug, which is convenient for quick adjustment and overall hanging. Operation and improve efficiency.